(1)സഹിഷ്ണുതശ്രദ്ധിക്കപ്പെടാത്ത ആകൃതി GB1184-80 ആവശ്യകതകൾ നിറവേറ്റണം.
(2) ശ്രദ്ധിക്കപ്പെടാത്ത നീളത്തിൻ്റെ അനുവദനീയമായ വ്യതിയാനം ± 0.5mm ആണ്.
(3) കാസ്റ്റിംഗിൻ്റെ ടോളറൻസ് സോൺ ശൂന്യമായ കാസ്റ്റിംഗിൻ്റെ അടിസ്ഥാന വലുപ്പ കോൺഫിഗറേഷനുമായി സമമിതിയാണ്.
വർക്ക്പീസ് മുറിക്കുന്നതിനുള്ള ആവശ്യകതകൾ
(1) ഭാഗങ്ങൾ പരിശോധിച്ച് പ്രവർത്തന രീതി അനുസരിച്ച് സ്വീകരിക്കണം. മുമ്പത്തെ പ്രവർത്തന നടപടിക്രമത്തിൻ്റെ പരിശോധനയ്ക്ക് യോഗ്യത നേടിയതിനുശേഷം മാത്രമേ അടുത്ത പ്രവർത്തന നടപടിക്രമത്തിലേക്ക് അവരെ മാറ്റാൻ കഴിയൂ.
(2) പ്രോസസ്സ് ചെയ്ത ഭാഗങ്ങളിൽ ബർറുകൾ ഉണ്ടാകാൻ അനുവാദമില്ല.
(3) പൂർത്തിയായ ഭാഗങ്ങൾ നേരിട്ട് നിലത്ത് വയ്ക്കരുത്, ആവശ്യമായ പിന്തുണയും സംരക്ഷണ നടപടികളും സ്വീകരിക്കണം. പ്രോസസ്സിംഗ് ഉപരിതലത്തിൽ തുരുമ്പ് ക്ഷയിക്കാൻ അനുവദിക്കില്ല, കൂടാതെ ബമ്പിൻ്റെ പ്രകടനം, ജീവിതം അല്ലെങ്കിൽ രൂപം, സ്ക്രാച്ച്, മറ്റ് വൈകല്യങ്ങൾ എന്നിവയെ ബാധിക്കും.
(4) റോളിംഗ് ഫിനിഷിംഗ് ഉപരിതലം, റോളിംഗിന് പുറംതൊലി പ്രതിഭാസം ഉണ്ടാകരുത്.
(5) അവസാന പ്രക്രിയയിൽ ചൂട് ചികിത്സയ്ക്ക് ശേഷം ഭാഗങ്ങളുടെ ഉപരിതലത്തിൽ ഓക്സൈഡ് സ്കെയിൽ ഉണ്ടാകരുത്. ഇണചേരൽ ഉപരിതലം പൂർത്തിയാക്കിയ ശേഷം, പല്ലിൻ്റെ ഉപരിതലം അനീൽ ചെയ്യാൻ പാടില്ല
(6) പ്രോസസ്സ് ചെയ്ത ത്രെഡ് ഉപരിതലത്തിൽ കറുത്ത തൊലി, മുട്ട്, റാൻഡം ബക്കിൾ, ബർർ തുടങ്ങിയ തകരാറുകൾ ഉണ്ടാകാൻ അനുവാദമില്ല.
BMT പ്രൊഫഷണൽമെഷീനിംഗ് ഭാഗങ്ങൾ
മെഷീനിംഗിലെ ഓപ്പറേറ്റർമാർ മെഷീനിംഗ് പ്രക്രിയയുടെ വർഗ്ഗീകരണവും മെഷീനിംഗ് പ്രക്രിയയുടെ സാങ്കേതിക ആവശ്യകതകളും മനസ്സിലാക്കുന്നു, മെഷീനിംഗിലെ പിശകുകൾ മികച്ച രീതിയിൽ കുറയ്ക്കാൻ കഴിയും. വലിയ ഫ്രെയിം വെൽഡിംഗ് പ്രോസസ്സിംഗിൽ ഏർപ്പെട്ടിരിക്കുന്ന റൈം ബില്ലിറ്റൺ മെഷീനിംഗ് പ്രത്യേകമാണ്.CNC ഗാൻട്രി മില്ലിംഗ്, ലാർജ് പ്ലേറ്റ് പ്രോസസ്സിംഗ് മെഷിനറി, ലാർജ് പ്രിസിഷൻ സിഎൻസി ലാത്ത് പ്രോസസ്സിംഗ്, ഹോറിസോണ്ടൽ സിഎൻസി മെഷീനിംഗ്, പ്രിസിഷൻ മെഷിനറി പാർട്സ് പ്രോസസ്സിംഗ്, ഷാസിസ് ഷീറ്റ് മെറ്റൽ പാർട്സ് പ്രോസസ്സിംഗ്, മെറ്റൽ സ്റ്റാമ്പിംഗ് പാർട്സ് പ്രോസസ്സിംഗ്, വലിയ മെക്കാനിക്കൽ പ്രോസസ്സിംഗ് പ്ലാൻ്റിൻ്റെ എല്ലാത്തരം വലിയ തോതിലുള്ള ഉയർന്ന കൃത്യതയുള്ള ഹാർഡ്വെയർ ഭാഗങ്ങൾ.
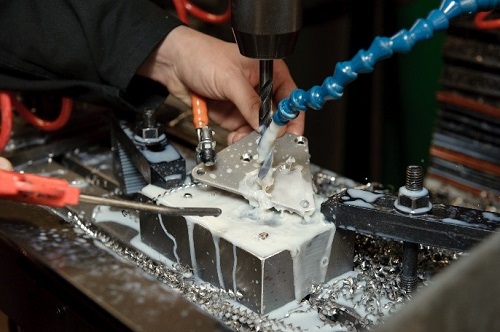
മെഷീൻ ടൂളുകളുടെ നിർമ്മാണ പിശകുകളിൽ സ്പിൻഡിൽ റൊട്ടേഷൻ പിശക്, ഗൈഡ് റെയിൽ പിശക്, ട്രാൻസ്മിഷൻ ചെയിൻ പിശക് എന്നിവ ഉൾപ്പെടുന്നു.
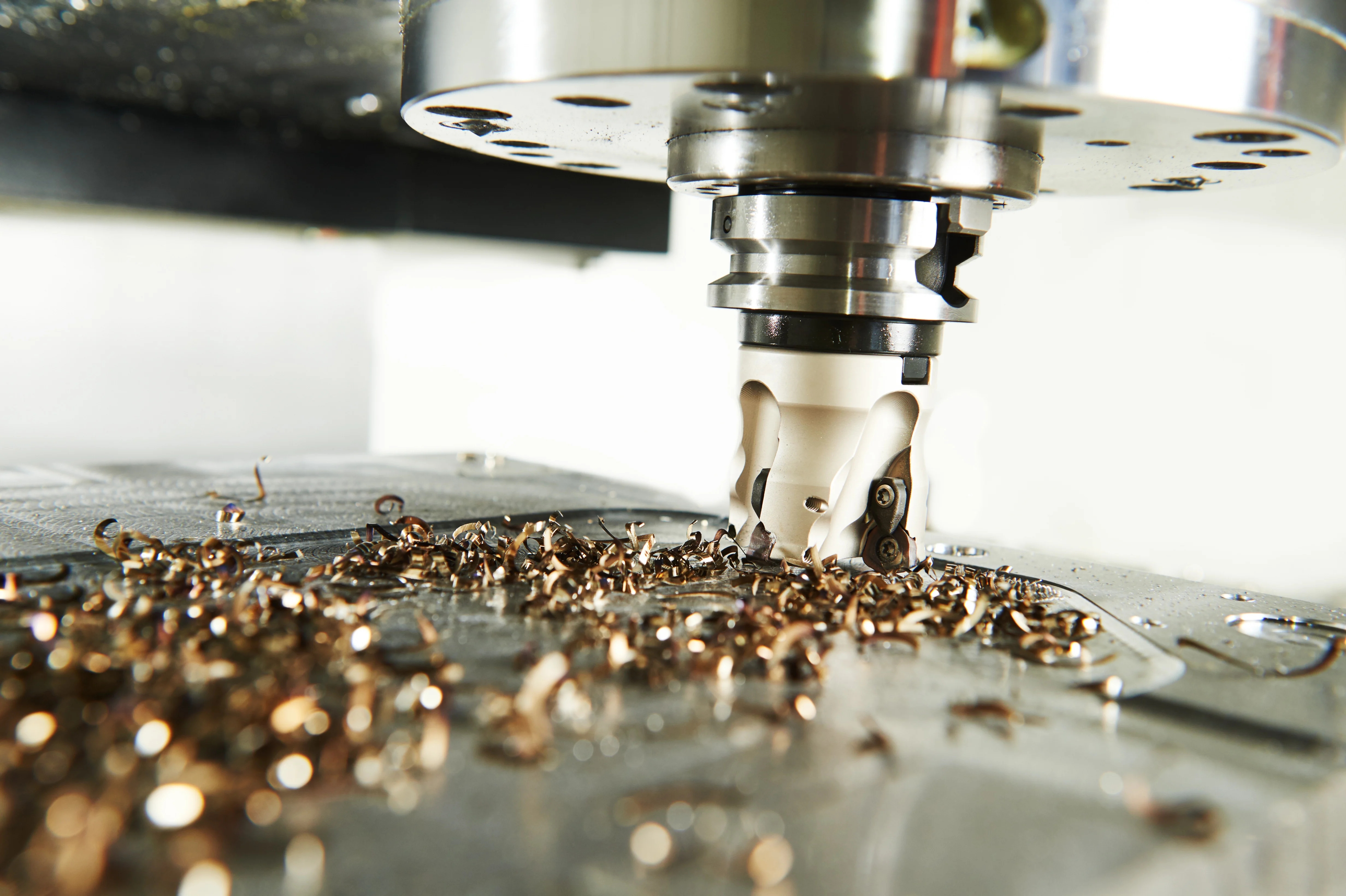
1. സ്പിൻഡിൽ റൊട്ടേഷൻ പിശക്
സ്പിൻഡിൽ റൊട്ടേഷൻ പിശക് എന്നത് മാറ്റത്തിൻ്റെ ശരാശരി ഭ്രമണ അക്ഷവുമായി താരതമ്യപ്പെടുത്തുമ്പോൾ ഓരോ നിമിഷത്തിൻ്റെയും യഥാർത്ഥ സ്പിൻഡിൽ റൊട്ടേഷൻ അക്ഷത്തെ സൂചിപ്പിക്കുന്നു, ഇത് പ്രോസസ്സ് ചെയ്യുന്ന വർക്ക്പീസിൻ്റെ കൃത്യതയെ നേരിട്ട് ബാധിക്കും. സ്പിൻഡിൽ റൊട്ടേഷൻ പിശകിൻ്റെ പ്രധാന കാരണങ്ങൾ സ്പിൻഡിലെ കോക്സിയാലിറ്റി പിശക്, ബെയറിംഗിൻ്റെ തന്നെ പിശക്, ബെയറിംഗുകൾക്കിടയിലുള്ള കോക്സിയാലിറ്റി പിശക്, സ്പിൻഡിൽ വൈൻഡിംഗ് മുതലായവയാണ്. ഗൈഡ് റെയിൽ ഓരോന്നിൻ്റെയും ആപേക്ഷിക സ്ഥാന ബന്ധം നിർണ്ണയിക്കുന്നതിനുള്ള ഡാറ്റയാണ്. മെഷീൻ ടൂളിലെ മെഷീൻ ടൂൾ ഭാഗം, മെഷീൻ ടൂൾ ചലനത്തിൻ്റെ ഡാറ്റയും ആണ്. ഗൈഡ് റെയിലിൻ്റെ നിർമ്മാണ പിശക്, അസമമായ വസ്ത്രധാരണം, ഇൻസ്റ്റാളേഷൻ ഗുണനിലവാരം എന്നിവയാണ് ഗൈഡ് റെയിലിൻ്റെ പിശകിന് കാരണമാകുന്ന പ്രധാന ഘടകങ്ങൾ. ട്രാൻസ്മിഷൻ ചെയിൻ പിശക് എന്നത് ട്രാൻസ്മിഷൻ ചെയിനിൻ്റെ രണ്ടറ്റത്തും ട്രാൻസ്മിഷൻ ഘടകങ്ങൾ തമ്മിലുള്ള ആപേക്ഷിക ചലന പിശകിനെ സൂചിപ്പിക്കുന്നു. ട്രാൻസ്മിഷൻ ശൃംഖലയിലെ ഓരോ ഘടക ലിങ്കുകളുടെയും നിർമ്മാണ, അസംബ്ലി പിശകുകൾ, അതുപോലെ തന്നെ ഉപയോഗ പ്രക്രിയയിലെ തേയ്മാനം എന്നിവ മൂലമാണ് ഇത് സംഭവിക്കുന്നത്.
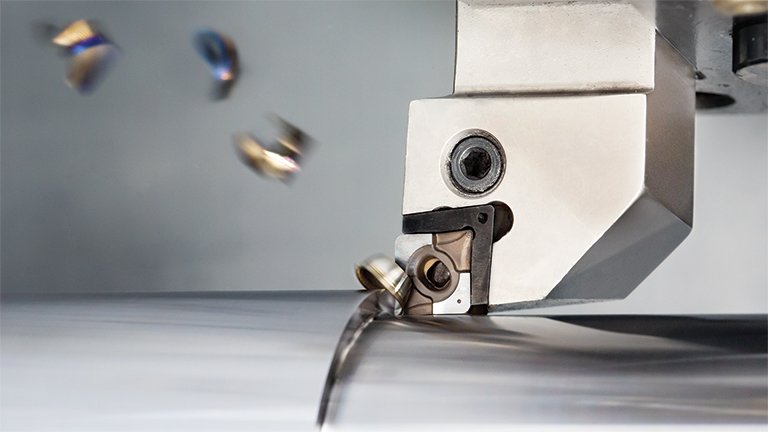
2. സ്ഥാനനിർണ്ണയ പിശക്
ലൊക്കേഷൻ പിശകിൽ പ്രധാനമായും ഡേറ്റം മിസ്കോൺസിഡൻസ് പിശകും ലൊക്കേഷൻ ജോടി നിർമ്മാണത്തിലെ കൃത്യതയില്ലായ്മയും ഉൾപ്പെടുന്നു. മെഷീൻ ടൂളിൽ വർക്ക്പീസ് പ്രോസസ്സ് ചെയ്യുമ്പോൾ, പ്രോസസ്സിംഗിനുള്ള പൊസിഷനിംഗ് ഡാറ്റയായി വർക്ക്പീസിലെ നിരവധി ജ്യാമിതീയ ഘടകങ്ങൾ തിരഞ്ഞെടുക്കേണ്ടത് ആവശ്യമാണ്. തിരഞ്ഞെടുത്ത പൊസിഷനിംഗ് ഡാറ്റയും ഡിസൈൻ ഡാറ്റയും (ഒരു ഉപരിതല വലുപ്പവും ഭാഗത്തിൻ്റെ ഡ്രോയിംഗിലെ സ്ഥാനവും നിർണ്ണയിക്കാൻ ഉപയോഗിക്കുന്ന ഡാറ്റ) പൊരുത്തപ്പെടുന്നില്ലെങ്കിൽ, അത് ഡാറ്റയുടെ പൊരുത്തക്കേട് പിശക് സൃഷ്ടിക്കും.
വർക്ക്പീസിൻ്റെ ലൊക്കേഷൻ പ്രതലവും ഫിക്ചറിൻ്റെ ലൊക്കേറ്റിംഗ് എലമെൻ്റും ഒരുമിച്ച് ലൊക്കേറ്റിംഗ് ജോഡിയെ ഉൾക്കൊള്ളുന്നു. ലൊക്കേറ്റിംഗ് ജോഡിയുടെ കൃത്യതയില്ലാത്ത നിർമ്മാണവും ലൊക്കേറ്റിംഗ് ജോഡി തമ്മിലുള്ള ഇണചേരൽ വിടവും മൂലമുണ്ടാകുന്ന വർക്ക്പീസിൻ്റെ പരമാവധി സ്ഥാന വ്യതിയാനത്തെ ലൊക്കേറ്റിംഗ് ജോഡിയുടെ കൃത്യതയില്ലാത്ത നിർമ്മാണ പിശക് എന്ന് വിളിക്കുന്നു. അഡ്ജസ്റ്റ്മെൻ്റ് രീതി ഉപയോഗിക്കുമ്പോൾ മാത്രമേ പൊസിഷനിംഗ് ജോഡിയുടെ നിർമ്മാണ കൃത്യതയില്ലാത്ത പിശക് ഉണ്ടാകൂ, പക്ഷേ ട്രയൽ കട്ടിംഗ് രീതിയിലല്ല.
പോസ്റ്റ് സമയം: ഓഗസ്റ്റ്-01-2021